CLOSE
About Elements
TANAKA is a leading company in the field of precious metals.
Advanced materials and solutions that support societal progress, the development stories behind them, the voices of engineers, and our management philosophy and vision—
Elements is an online media platform that shares insights that lead to a better society and a more prosperous future for the planet under the slogan “Mastering Precious Metals.”

Bondability and Reliability of Palladium-Coated Copper Wires
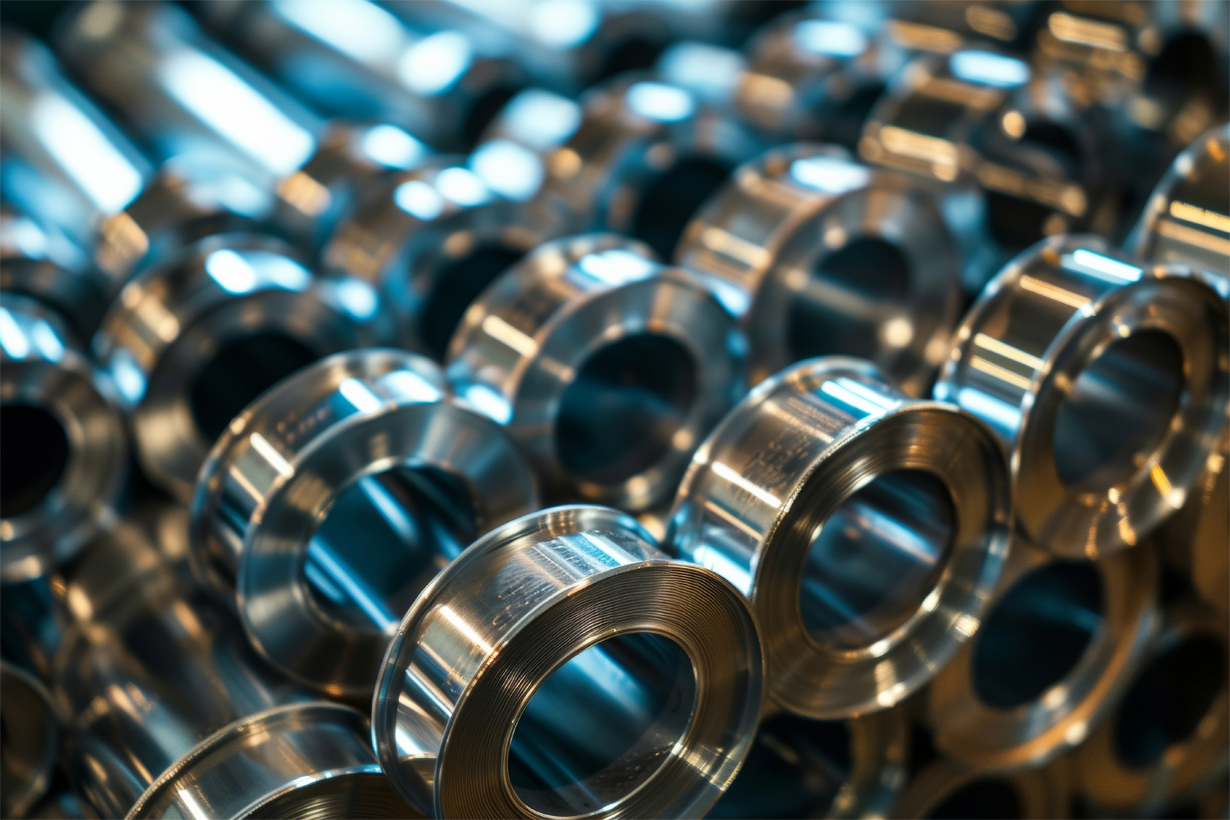
Semiconductor Digest April/May 2024
DODGIE CALPITO, Tanaka Kikinzoku International (America),
TAKESHI KUWAHARA and YUKI ANTOKU, Tanaka Denshi Kogyo K.K. (Japan)
High-reliability CHR PCC wires have proprietary doping that cause the original Pd coating to remain at the surface of the ball.
Pd at the ball bond surface on Al pads form ternary intermetallics with Cu9Al4 that prevent corrosion and bond failure.
BESIDES SILVER, COPPER (CU) IS THE MOST
conductive metal known to exist, making it ideal for bonding wires used to interconnect semiconductors. However, it is highly prone to oxidation or corrosion attack by highly reactive halogens such as chlorine. Chlorine (Cl) is present in uncontrolled environments or even in electronic molding compound used to encapsulate semiconductors.
Because of this, Palladium-Coated Copper (PCC) bonding wire was developed and has now become the most dominant bonding material used in fine wires of diameters of <50 microns being used as substitute for more expensive gold.
Thermosonic wire bonding is the most popular form of interconnection for most semiconductors. It requires the creation of a molten Free-Air Ball (FAB) at the end of the wire that is then ultrasonically-pressed on semiconductor bonding pads to form the first bond.
When using PCC wires however,forming gas is needed during the FAB formation to prevent the oxidation of Cu that is usually exposed during the process. The exposure of Cu is caused by the Pd coating flowing within the FAB due to differences in surface tension between the component metals (an earlier article entitled “Tanaka — Tears of Wine and Palladium-coated Copper Wire — The Marangoni Effect” describes this phenomenon — see the March issue of Semiconductor Digest, pp. 33-34).
In the past year, Tanaka has started production of a new series of high-reliability PCC wires which prevents Pd flow and thus maintain its coverage of Cu on the FAB during formation.
This article presents comparison between conventional and high reliability PCC wire in terms of bondability and reliability.