해결 사례
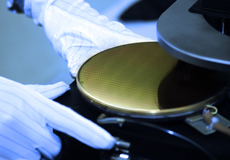
리사이클에 의한 재료 사용률 향상 계획
소형, 경량화가 대명제인 차세대 기술 개발.
「재료의 리사이클」이라는 새로운 발상으로 프로젝트를 성공으로.
반도체 메이커 Y사
배선의 극세화가 잘 진행되지 않고 제품화가 어렵다…
전자기기의 소형화, 경량화는 메이커로서 지상 과제가 되었습니다. 이것에 대응하기 위해 반도체 디바이스에도 소형화나 대용량화 등이 요구되고 있으며, 배선의 미세화 등 많은 과제가 있습니다.
Y사에서도 메이커로의 요구로 차세대 디바이스의 개발이 요구되고 있었습니다.
“작은 것이 당연시되는 요즘, 당사에서도 요구되는 제품은 더욱 데이터 용량이 큰 디바이스의 개발이었습니다. 그렇지만, 기술 과제의 하나인 배선의 미세화가 제대로 되지 않았던 것입니다. 그도 그럴 것이, 미세화에 의해 배선을 형성하는 공정에서의 제품 수율이 악화하는 등의 문제가 발생하여 설계한 대로 디바이스를 제작할 수가 없고 제품화할 수 없는 상황이었습니다.”라고 개발 담당인 K씨는 말했습니다.
또한, 길어지는 연구개발이 비용을 압박. 납기가 다가오는 가운데 처음부터 새로운 것에 착수할 만한 여유도 없어서 곤란한 상황이었습니다.
재료 특성을 살려 개발에 성공!
어떻게든 타개책을 찾기 위해 다른 부서의 동료에게 상담한 K씨는 다나까귀금속의 담당자를 소개받았습니다. K씨가 개발 중인 제품에 대해 상담을 하자, “같은 재료라도 더 순도가 높은 것으로 시험해 보면 어떨까요?”라는 제안을 받은 것입니다. 자세한 얘기를 들어 보니 “다나까귀금속이라면 불순물을 제거한, 더 순도가 높은 재료를 공급할 수 있습니다.”라는 것이었습니다.
그래서 이제까지 사용하던 것보다 순도가 높은 것으로 샘플을 제작하기로 했습니다. 그 결과, 순도가 높아짐으로써 문제가 해소되었고, 제품으로서 출시할 수 있는 수준까지 간 것입니다.
개발에 성공! 그렇지만, 예상치 못한 비용이…
그렇지만, 본격적인 제품화를 검토하는 단계가 되었을 때 예상치 못한 문제가 있었던 것입니다. 그것은 디바이스 제조 공정의 재료 손실이 많아서 예상했던 것 이상의 비용이 든다는 문제였습니다. “통상 이들 재료 중에서 실제로 사용되는 것은 전체의 10% 정도입니다. 나머지는 모두 낭비하게 되므로, 이 상태로 대량생산을 하기에는 비용이 너무 많이 들었습니다.”라고 K씨는 말했습니다.
K씨는 다나까귀금속의 담당자에게 비용 상담을 했습니다. 그러자 담당자로부터 의외의 대답이 돌아온 것입니다.
재료를 회수해서 비용도 손실도 절감
그 대답이란 “재료를 낭비하지 않으므로 비용 걱정도 필요 없습니다.”라는 것이었습니다. 다나까귀금속의 재활용 시스템으로 지금까지 폐기하던 것의 90%를 원래의 신규 재료와 동등한 순도로 재정제해서 재사용할 수 있다는 것이었습니다. ‘재활용을 한 경우의 재료 사용률을 고려한 총비용 제안’을 받은 Y사는 배선 형성 공정에서의 비용을 30% 절감하는 것에 성공. 제품화 후의 안정 공급에 대한 목표가 세워져 의뢰처의 메이커도 대단히 만족하는 제품을 납품할 수가 있었던 것입니다.
“재료 부문이므로 모든 것을 알고 있다고 생각했습니다. 그래도 역시 떡은 떡집에 맡겨야 하네요. 재료에 관해서는 재료의 프로에게 묻는 것이 제일이라고 생각했습니다.”. K씨는 디바이스를 개발할 때는 재료 선정 시부터 다나까귀금속에 상담한다고 말해 주었습니다.