Case Study
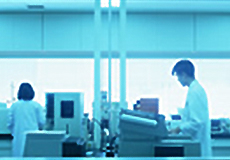
High Precision, High Durability, Low Cost Bead Dishes
End-customer complained about a drop in precision of component analysis.
So what was the secret to achieving high precision, high durability and low costs?
Company W (Quality Assurance Dept. of ceramics manufacturer)
Aging of the component analysis bead dishes was the cause, so what did Company W do?
Company W, a ceramics manufacturer, carries out its own raw material testing prior to manufacture. Using platinum alloy bead dishes, they vitrify the raw material before X-raying the material to analyze its components.
One day, Company W’s sales department received a telephone complaint from one of its customers. “Our people have been complaining that the products we’ve been receiving from you lately are poor quality. What are you going to do about it?”
The salesperson quickly replaced the problem products for the customer, but this had never happed before so he asked his manager to look into the cause. Management immediately ordered the relevant departments to find the cause because complaints like this could quickly lead to industry-wide rumors that Company W’s products cannot be used, which could also threaten the continued existence of the company.
After a few days without finding the cause of the drop in quality, the Quality Assurance Department issued a report on their investigation. It explained; “We suspect that products were still being manufactured even though correct analysis was not possible due to aging of the bead dishes used for component analysis of materials, which resulted in those products being of poor quality.”
Because the material is heated at high temperatures of 1,100–1,200°C to produce the glass samples, the bases of the platinum alloy bead dishes became severely damaged and deformed, so Company W was recycling them about once every three months and replacing them with new dishes. However, the Quality Assurance Department believed the latest analysis must have required a faster turnaround and the dishes were not replaced as often, which lead to the current complaint. Other departments at Company W continued looking for another cause as well, but since there were no other apparent causes reported, the Quality Assurance Department proceeded to replace the bead dishes to attempt to achieve correct analyses.
Company W had been using platinum alloy bead dishes in the past, but they had only lasted three months. They started looking for a supplier, other than the one they had been using, to supply them with high durability bead dishes. At the same time though, they wanted to hold down costs. To prevent another complaint like the previous one, they needed dishes that would enable them to achieve the correct values for as long as possible. Even though the quality assurance team located a number of companies who could provide the bead dishes, they were unable to finally decide on a new supplier. They decided to sit down and talk to each of them.
Durability and high precision, but at half the cost

Platinum Dishes, Bead Dishes
One of the selected companies was TANAKA, a company deeply involved in the manufacture and sale of precious metal products for industry. TANAKA’s proposal was to use an even more durable oxide-dispersion-strengthened material, and to improve the glass release characteristics by changing from hand polishing to mechanical polishing. The proposal would produce longer-life bead dishes that enabled stable quality even at high temperatures.
TANAKA’s salesperson told Company W that, “Another customer praised the dishes, saying that despite the higher initial cost of bead dishes using strengthened material, durability is improved and total costs are reduced through the improved durability, in addition to which product wall thickness variations are reduced to enable uniform heating.”
Company W spoke to other companies as well, but they decided that Tanaka’s products offered better costs and performance, so they placed their order with us.
Reasons for choosing TANAKA products
- High durability, using oxide-dispersion-strengthened material
- High precision manufacturing, with uniform wall thickness
- Low cost, reducing total costs by reducing the frequency of replacements
After 1 year using TANAKA’s bead dishes, the Quality Assurance Department of Company W appreciates the stable performance of the new bead dishes, far exceeding that of the previous platinum alloy bead dishes. The company had previously replaced their bead dishes about once every three months, but the new dishes last about one year, which has enabled them to reduce total costs by as much as 50%.