解決事例
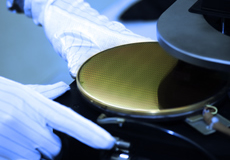
リサイクルによる材料使用率向上プラン
小型・軽量化が大命題の次世代技術開発。
「材料のリサイクル」という新発想でプロジェクトを成功に。
半導体メーカーY社
配線の微細化に難航。長引く研究開発がコストを圧迫。迫る納期…
電子機器の小型化、軽量化はメーカーにとって至上命題となっています。これに対応するため半導体デバイスにも小型化や大容量化などが求められており、配線の微細化など多くの課題があります。
Y社でも、メーカーからの要望で次世代デバイスの開発に追われていました。
「小さいことは当たり前の今、弊社でも求められる製品はよりデータ容量の大きなデバイスの開発でした。しかし、技術課題の一つである配線の微細化がうまくいかなかったのです。というのも、微細化によって配線を形成する工程での歩留まりが悪化するなどの不具合が発生してしまい、設計どおりのデバイスを作製できずに製品化できない状況でした」と、開発担当のK氏は語ります。
さらに、長引く研究開発がコストを圧迫。納期が迫る中、一から新しいことに着手できるだけの余裕もなく、
困ってしまいました。
不純物を取り除き、より純度の高い材料で不具合を解消
なんとか打開策はないかと他部署の同僚に相談したK氏は、田中貴金属の担当者を紹介されました。K氏が開発中の製品について相談をすると、「同じ材料でもより純度の高いもので試してみてはいかがでしょうか」という提案を受けたのです。詳しく話を聞いてみると、「田中貴金属なら、不純物を取り除いたより純度の高い材料を供給できます」ということでした。
そこで、これまで使用していたものよりも純度の高いものでサンプルを作製することにしました。その結果、純度が高くなったことで不具合が解消し、製品として世に送り出せるレベルまでいったのです。
製造プロセスでの材料ロスから、想定以上のコストがかかることが判明…
ところが、本格的な製品化を検討する段階になって、思わぬ落とし穴があったのです。それは、デバイス製造プロセスでの材料ロスが多く、想定以上のコストがかかってしまうという問題でした。
「通常、これらの材料で実際に使用されるのは全体の10%ほどです。残りはすべてムダになってしまうため、今のまま大量生産をするにはコストがかかりすぎました」とK氏は語ります。
K氏は、田中貴金属の担当者にコストの相談をしました。すると、担当者からは意外な答えが返ってきたのです。
「材料リサイクルシステム」を導入、トータルコスト30%カットに成功
その答えとは、「材料をムダにしませんから、コストの心配もありません」というものでした。田中貴金属のリサイクルシステムで、今まで廃棄していたものの90%を、元の新しい材料と同等の純度に再精製し、再利用することができるというものでした。
「リサイクルをした場合の材料使用率を考慮した、トータルコスト提案をしてもらいました」
Y社は、配線形成のプロセスにおいてのコストを30%カットすることに成功。製品化後の安定供給の目処がたち、依頼先のメーカーも大満足のものを納めることができたのです。
「開発部門なので、すべてを知っているつもりでいました。それでもやはり、餅は餅屋ですね。材料のことは材料のプロに聞くことが一番だと思いました」
K氏は、デバイス開発の際は、材料の選定時から田中貴金属に相談していくと語ってくれました。