解決事例
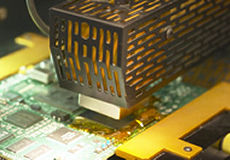
製造装置へのめっき加工
もはや限界かと思われた「生産性の向上」と「コスト削減」。
生産ラインの停止を1/3に抑えた「めっき加工」とは?
半導体メーカーA社
市場の拡大が著しい半導体市場。盛り上がりの裏では、海外メーカーを含めた競争が激しく、各社、生産性の向上とコスト削減が重要課題となっています。今までと同じレベルでの企業努力では既に限界が見えはじめ、新たな取り組みが求められています。
残されたコスト削減の可能性は、年6回の生産ラインの部品交換
半導体市場が回復しているこの時期に、一気にシェアを取りにいきたい半導体メーカーA社。そのために生産性の向上とコスト削減は重要課題となっていました。しかし、これまでもそういった取り組みは行ってきており、大部分の改善はやりつくしていました。そこで、更なる生産性の向上とコスト削減を実現するために、プロジェクトを立ち上げることにしました。
このプロジェクトに抜擢された開発部のTさんは、生産ラインの現状調査からはじめました。調査開始後すぐに、Tさんは1つの問題点に気づきました。それは、1年間に6回生産ラインを停止するため、生産性が下がってしまうという問題でした。A社の半導体製造過程には、800℃という高温で熱する工程があります。この工程では高温で処理を行うため製造装置自体に負荷がかかり、内部の腐食や損傷が進みやすくなります。そのため、生産ラインを停止し部品を交換する必要があったのです。
部品交換による生産ラインの停止に関しては、以前からA社内で重要課題となっていました。交換の度に数百万円という費用がかかるものの、部品交換を行わなければ半導体の品質低下が著しく発生してしまいます。万が一、半導体に粗悪品が混ざっていた場合、クレームに発展しA社の信用問題にもなりかねません。そのため、A社では経営陣を含め、この部品交換はやむを得ないものと考えられてきました。
今まで以上の取り組みを求められている開発部のTさんにとって、ライン停止時の機会損失を改善することができれば、プロジェクトを成功させることができます。こうしてTさんの挑戦ははじまりました。
製造装置そのものへの「めっき加工」で、ラインの停止期間を1/3に!
開発部のTさんは、生産ラインにおける「生産性の向上とコスト削減」に挑戦すべく、情報収集をはじめました。半導体業界の展示会やセミナーへの参加、インターネットでの検索等々・・・。しかし、これといった有益な情報を得られず焦りを感じていた頃、別案件で取引をしている田中貴金属の営業担当から、ある情報を得ることができました。
「製造装置にめっき加工すると、耐久性が向上し、生産ラインの停止を低減できます。」
A社は、田中貴金属にチタン電極への白金めっき加工を依頼していましたが、製造装置自体にめっき加工を行うという発想は、今までにありませんでした。田中貴金属の営業担当によると、製造装置自体へのめっき加工は腐食や損傷を抑えることができるので、生産ラインの停止頻度を下げることができ、稼動停止期間も今までより短縮することができるとの事。
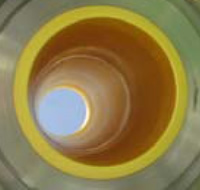
製造装置の内面に10μm厚の
金めっきを実施
今まで考えつかなかっためっきの利用方法に、開発部のTさんは驚きと同時に大きな期待を抱きました。実行してみる価値は大いにある提案内容だったので、なんとか経営陣の承諾を得て、早速、田中貴金属に依頼をすることに・・・。
現状の製造装置自体の部品交換では、生産ラインの稼動停止は1年間に6回発生していましたが、今回新しく採用した「製造装置の高熱を発する部分だけにめっき加工する方法」では、製造装置の腐食や損傷を抑えることができるため、部品の交換は、1年に2回と1/3にまで抑えることができました。さらには、コストも従来の約40%削減できました。
「生産性の向上とコスト削減」を実現できたTさんはプロジェクトを成功へと導くことができました。こうして競争力を強化できたA社は、競合他社より市場シェアの獲得を一歩リードすることができました。
田中貴金属では、製品を加工し納品して終わりではなく、製品寿命を全うした製造装置などの廃棄物や製造現場から発生したスクラップから貴金属を回収し、製品として市場に戻すといったリサイクルも行っていました。Tさんは、次の装置交換のときにこの装置の金めっきを有効に活用しようと、リサイクル部分も田中貴金属にお願いしたいと考えています。